Inside Logitech: How headsets are designed and tested
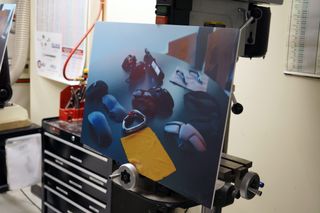
When discussing gaming headsets, it’s rare to hear the praise “it sounds good” without the qualification “...for a gaming headset” tacked onto the end. There’s a stigma around gaming audio gear that even the best cans fall short of real headphones. And that stigma’s often justified, thanks to cheaper components or build quality and drivers tuned to enhance bass over balance. Logitech’s trying to break that curse with its new Artemis Spectrum headsets, and to reinforce the point that the new headsets sound great, period, they invited a group of journalists to Logitech’s Camas, Washington audio facility to see how the headset was made.
Last year I toured Logitech’s Swiss headquarters to see how gaming mice are built and tested. This was a similar tour chronicling the development of the Artemis Spectrum, from material design through acoustic engineering, acoustic testing in a million-dollar anechoic chamber, electrical testing, and finally surround sound design.
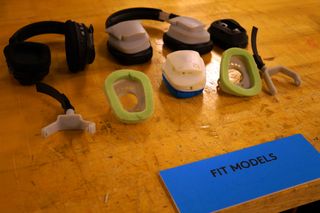
“We did a ton of fit models,” says global product manager Doug Sharp. Sharp has experience in a number of roles, including industrial design, and spoke passionately about everything from the shape of the headset, to the materials used in prototyping and final hardware, to sound quality. He’s a bit of an audiophone himself.
“There was probably 3 or 4 months of fit. There’s always a lot of friction between the different departments as far as the goal, and I think that’s really good, because we’re stretching and reaching. When you look at the design for the G33 and the 633, you’ll see that it has this sweeping curve when you look at the silhouette of the design. This is really different from the G930. It was a very straight up-and-down, almost symmetrical design, which doesn’t look as neat. So when we went into the fit structure and test, we had to do tons of angling so that we could still have the center of force be right on the earcup, because you want it to fit very tightly all around your ear. You don’t want extra pressure around the front or the back, and everyone’s head is very different, right? We want it to fit the most people in the best way.”

Logitech talked about retaining the fit of its popular G930 headset. The new headset has a different look and shape, but retains a similar fit. Here you can see some early models of the headset before it went into final production.
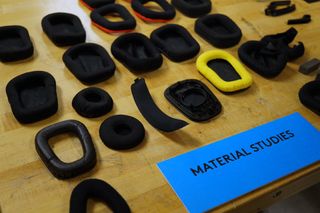
Logitech tested a variety of materials for the new headset, testing for comfort, fit and sound quality. A lot of things about materials can affect each of those criteria. For instance, Logitech originally used a rounded earcup material, which feels smooth and looks very slim. But that rounded earcup doesn’t isolate sound as well as a flat-stitched earcup, because there’s less surface area making contact with your head. It’s not quite as sexy, but makes for better audio quality. So they switched to the flat stitching used in the final Artemis Spectrum.
“People love the 930 [headset], it has very good isolation, but we wanted to have something that absorbed more sweat, that you could wear longer, and felt lighter, and breathes better,” said Doug Sharp. “We did a ton of materials research, we actually looked at the materials and did the analysis for heat absorption and heat dissipation, to see which material would release the most heat off your head to give you that better experience. The one we came up with, once we got it into a head mount, it didn’t feel better than what we had. So we went to a slightly softer material with about 95% efficiency, but it feels a lot like velvet on your head. Little tiny compromises, but these are all the things we’re thinking about constantly.”
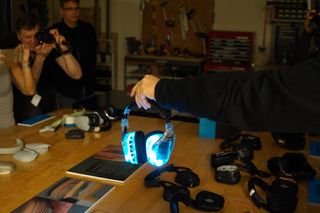
Logitech built LEDs into the earcups of the Artemis Spectrum. This model uses transparent plastics on the earcup, and was used to test the light distribution of the LEDs. The final model uses black plastic around the earcups, with narrow strips of visible LED running around the border of the headset.
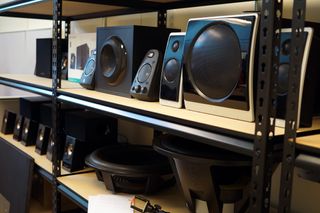
Speakers, speakers, and more speakers line the shelves at Logitech. Also: real big speakers. The Camas, Washington office also produces the UE Boom products. The office’s roots actually date back to Labtec, which Logitech acquired in 2001. Labtec made audio gear stretching back into the 1980s.
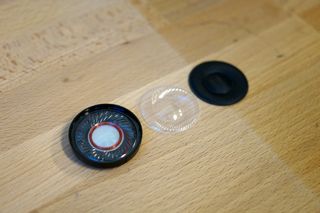
Logitech’s new Pro-G driver, which it designed for the Artemis Spectrum headsets. It’s a 40mm driver with a 20Hz-20KHz like the one used in its previous G930 headset, but not all 40mm drivers are created equal. Logitech’s seeking a patent for the Pro-G driver due to a new material it’s using for the diaphragm. More on that in a few slides.
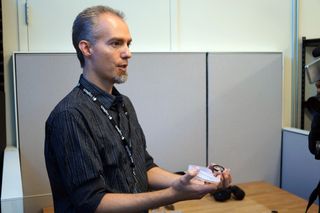
Senior acoustical systems engineer Tracy Wick shows off how a driver fits into the enclosure of a G930 headset.
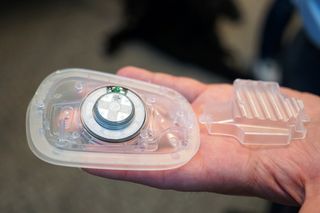
“Many companies use acoustic measurements to quantify performance, which is fantastic. We do that too,” says Tracy Wick. “But it’s not quite enough when you really want to squeeze all the juice out of driver design. So we did the same computer optimization on the enclosure section, which has calculated openings in the right size area of the right size length.”
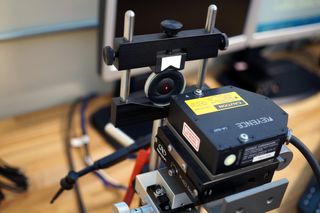
A laser pointed at the Pro-G driver used in Artemis Spectrum. Wick explains that “the laser is a displacement meter. It tells us where it is relative to zero. That allows us to optimize where the coil is within its travel, what’s its rest position, what are the maximums and minimums you can go to on this driver.”
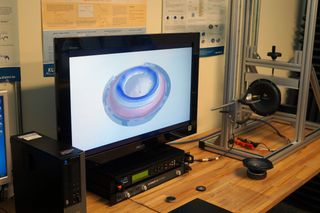
This display shows the cone movement of a headphone driver tested with the gear Logitech has in its lab. While this is just a still image, I got to watch the movement of the driver, fluctuating up and down as it produced sound. At lower frequencies, this movement was smooth and even. But at higher frequencies, things got messy.
Wick explains: “In the low frequency range, it’s very linear. It’s like an engine. The piston moves up and goes down. All points of the piston move the right way at 100 Hz. As we go up to 600 Hz, things are also very normal, but you’re starting to see a little bit of the rocking mode where one side will come up first. This is anticipated behaviour you see on a lot of drivers. Once you go to the voice band at 2600 Hz, there’s a problem. There’s a big giant dip, and you can directly correlate the frequency that does this to the amplitude measurement at each frequency.
“This lets us say, hmm, another solution is required to get really good fidelity. Our answer is the Pro-G driver.”
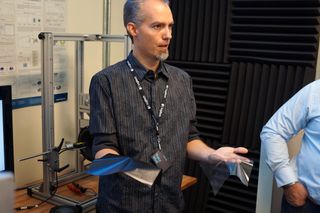
Wick shows off the new material (that black sheet in his right hand) Logitech used for the diaphragm of the Pro-G driver.
“You make diaphragms from a giant roll of mylar, basically,” Wick says. “You put it through a heat stamping machine and it will create the diaphragms. We just changed out the material and then optimized the system. That’s Artemis Spectrum. The old material is technically PET, but essentially it’s a homogeneous material. A solid. Ours is not. It is a composite of multiple layers. And that allows us to have the vibrations either damped or distributed to provide that smooth frequency response.”
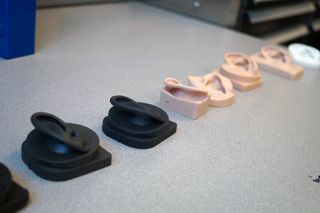
A set of model ears used to test headsets. They’re not just different sizes, but different materials. They use these to determine factors like the shape and depth of a headset earcup and measure sound performance.
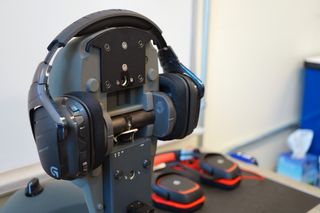
The ear models fit onto this dummy, which has microphones mounted inside it to measure the sound produced by the headset. This way Logitech can exactly measure the same sound a human listener would hear—minus all that psychoacoustic stuff that happens in our brains, which a microphone can’t replicate.
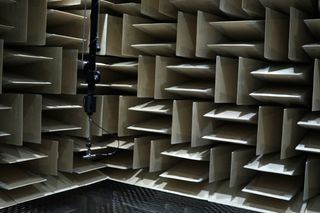
Inside the audio lab is a million-dollar anechoic chamber, which was built on its own foundation separate from the rest of the facility.
“On top of the foundation are 200 compression springs so that seismic activity, big trucks or whatever may happen outside, won’t get through to here,” says acoustics engineer Matt Green. “The roof has special treatment for noise rejection. Everything about this room helps keep echo from occurring. If we turn everything off in here, we do reach 0 dB, which is absolutely no sound a human can perceive. Which can get a little eerie for people.”
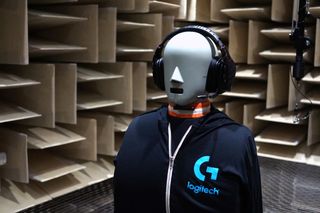
There are two mics inside this dummy named HATS (Head and Torso Simulator) inside the same ears we saw outside the chamber. He also has a speaker in his mouth modulated to produce sound similar to human speech, which allows Logitech to test their microphones and headset speakers simultaneously.
They also use the chamber to test features like sound leakage. They’ll place a large loudspeaker in the room and measure how much sound penetrates the headset, and will also set the headset to full blast and measure how much sound leaks out into the room.
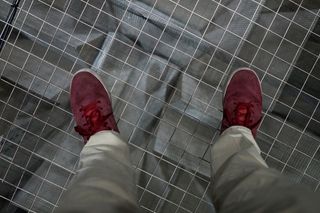
Steel wiring suspended above the anechoic fins feels a bit like walking on a trampoline. Sadly, there’s a no jumping policy in the anechoic chamber.
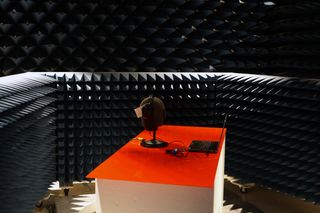
This similar-looking chamber is used to study wireless frequencies rather than sound. Wireless headsets have to meet FCC qualifications as well as European restrictions on emissions. The table sits on a spinning platform, and an antenna monitors the emissions profile of any electronic device placed on the table. This allows them to identify problematic emissions and tweak the signal to bring it in line.
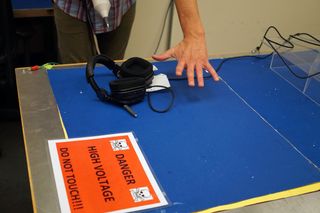
This room is used to test electronics, including headsets, for susceptibility to power surges and electrostatic discharge. The table is a horizontal ground plane, which is connected to another ground. They metal tip pictured can produce a significant discharge directly to a metallic point on the device (say, the headphone jack) up to 4000 volts. The goal of the testing is to ensure a device will continue functioning after taking a nasty zap.
This kind of testing sometimes leads to design changes; ports that are recessed to decrease the risk of a direct discharge, or little plastic flaps over what would be exposed metal. It could also affect changes to the electronics layout of a device, like adding more ground.
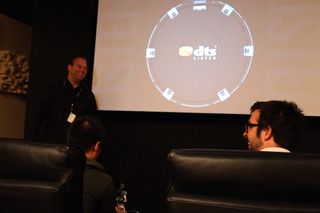
I wrapped up my tour of Logitech’s audio facilities by sitting in a perfectly tuned 7.1 surround sound theater room, which the company uses to build virtual surround profiles. The DTS Headphone:X demo in here was amazing, and made me a believer in virtual surround. We ran through three sound tests, hearing positional sound come through each of the seven speakers in the room. Then we listened to the same demo with the Artemis Spectrum headset on...and the positional audio sounded identical. The other journalists I demoed with had the same reaction: “did that actually come through the headset?”
Listening with one ear in, one ear out confirmed that we were indeed hearing the positional audio through the headset, and it was just about indistinguishable from the real thing.
The downside is that for the virtual surround to work this well in real use, games and other media will have to make use of DTS Headphone:X. The DTS drivers for the Logitech G633 and G933 headsets launch on September 20th, and once they’re out in the wild, I plan to spend more time testing them—and hope game audio engineers give the technology a shot.
Wes has been covering games and hardware for more than 10 years, first at tech sites like The Wirecutter and Tested before joining the PC Gamer team in 2014. Wes plays a little bit of everything, but he'll always jump at the chance to cover emulation and Japanese games.
When he's not obsessively optimizing and re-optimizing a tangle of conveyor belts in Satisfactory (it's really becoming a problem), he's probably playing a 20-year-old Final Fantasy or some opaque ASCII roguelike. With a focus on writing and editing features, he seeks out personal stories and in-depth histories from the corners of PC gaming and its niche communities. 50% pizza by volume (deep dish, to be specific).