How motherboards are made
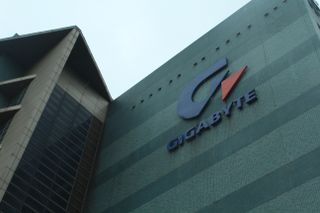
On an overcast (but stiflingly humid) Thursday afternoon in Taipei, Gigabyte shipped me out to their Nan Ping factory, about an hour out of town. This is one of three motherboard factories belonging to Gigabyte, with the other two – Dong-Guan and Ning-Bo – situated in China. As a Taiwanese company, Gigabyte is proud enough of their local manufacturing plant that they’ll invite media along – cameras and all.
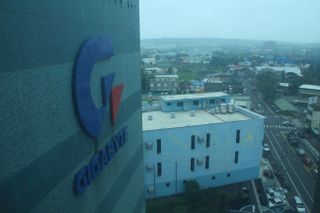
Nan Ping opened in 2000 and was the only motherboard factory in Taiwan at the time. It employs 1,150 people, with a reported 70 per cent of those with more than ten years experience in the manufacturing industry. According to our amiable host Herbert, motherboards are built “from 0 to 100 per cent” at Nan Ping. The nine floor complex doles out 575,000 motherboards per month, with each of these function tested before shipping.
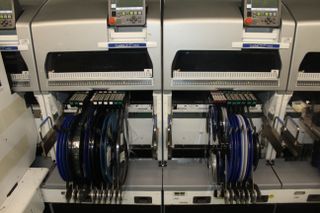
Herbert let us visit three floors on the tour. It was a bit rushed as the tour had started late, but it was enough to get a general idea of how motherboards are made. On the seventh floor was the SMT (Surface Mount Technology) assembly line, which is where all the automated magic happens. Basically, a series of monstrous machines are responsible for slotting the tiny resistors and chips you usually don’t notice. The one above feeds the necessary components into the fitting machine…
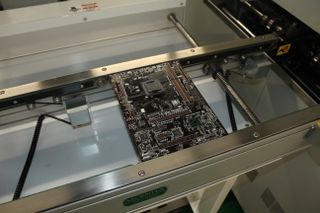
...and this is part of the conveyor which feeds the SMT machines with the printed circuit boards (PCBs). Parts are applied at frighteningly quick speeds.
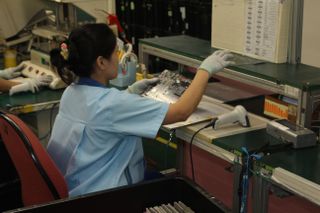
At the end of the line, workers are responsible for making sure the machines are holding up their end of the deal.
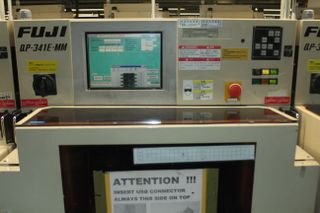
This is the tank-like beast responsible for all this sorcery. It can place pieces at 0.5 of a second. Which is quick enough, I suppose.
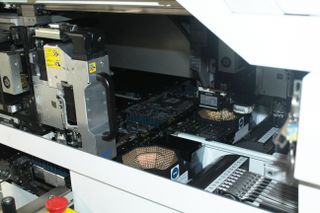
A peek inside one of the SMT behemoths.
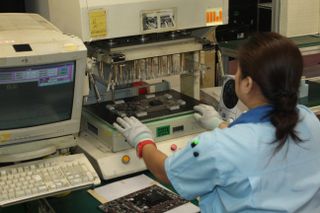
You don’t need 4K G-Sync enabled monitors to get the job done at the Gigabyte factory.
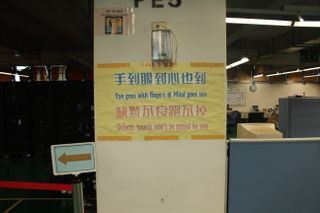
A little bit of production line pep talk. Feeling inspired?
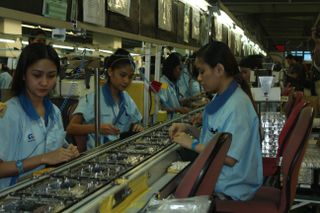
Down on the fifth floor is the DIP, or Manual Assembly Line. This involves a vast number of workers sitting elbow to elbow, carefully but rapidly fitting components into the motherboard that can't be automatically applied. I noticed some workers were fitting more than one component at a time.
It’s hard to imagine when looking at your motherboard, but yes, real human labour is involved, and quite strenuous, detailed labour at that.
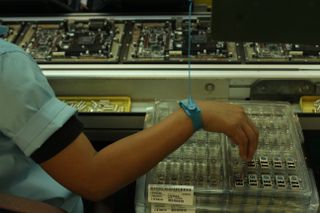
A production line worker wearing an anti-static wristband prepares to fit a panel of USB ports.
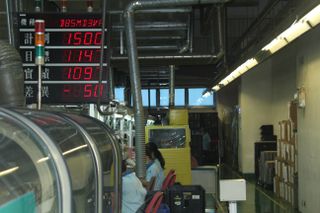
These are the targets for this particular manual assembly line. The top line is the model name, the second is the planned number of units, the third the target, and the fourth how many done already. The last line is the difference.
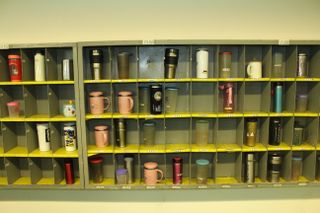
And this is where the workers keep their tea cups. Look at all of the beautiful tea cups.
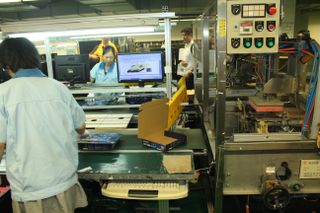
Down on the second floor is the packing, which is a mix between machine automation and handcraft. Basically, an empty box is fitted with each of its items, by workers, as it scrolls down the conveyor. Above is the beginning of the process.
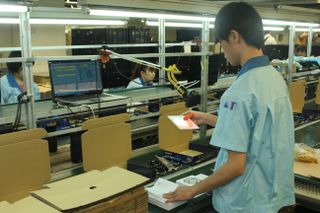
This worker is responsible for putting the manual and driver disc in each of the boxes.
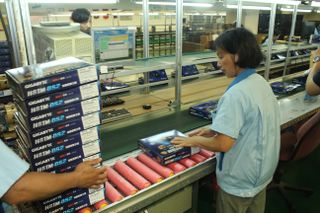
The boxes are sealed by hand...
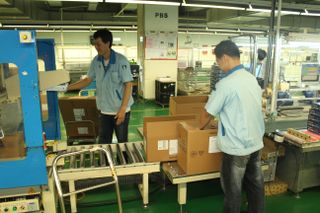
...and then readied for shipping.

Away from the shouting of Computex in nearby Taipei, the factory tour was an interesting insight into what actually needs to happen – not marketing, not branding, but actual component building – in order to run a PC.
Shaun Prescott is the Australian editor of PC Gamer. With over ten years experience covering the games industry, his work has appeared on GamesRadar+, TechRadar, The Guardian, PLAY Magazine, the Sydney Morning Herald, and more. Specific interests include indie games, obscure Metroidvanias, speedrunning, experimental games and FPSs. He thinks Lulu by Metallica and Lou Reed is an all-time classic that will receive its due critical reappraisal one day.